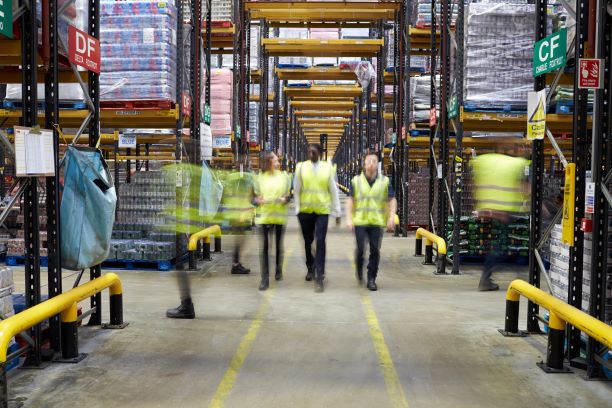
Product Identification and Productivity – is there a Connection?
Cold Chain Federation member The Supply Chain Consulting Group advise us on how they can help.
The receiving and storing of goods in the warehouse and their subsequent dispatch are all activities that have the potential to introduce delays. As each inbound shipment arrives the goods need to be identified, quality checked, sorted, recorded, and moved to their temporary location. When goods are ready to be dispatched, they need to be retrieved, grouped, packaged, and recorded before loading.
All these activities can derail any attempts at improving productivity. One of the main causes of warehouse delays is poor product identification (ID). There is often no consistency in how a product is identified throughout the supply chain. There can be multiple versions of that product ID existing in internal supply chain systems and in those at suppliers, carriers and other partners.
Product labelling
One of the main aims of labelling is to identify products. All relevant information about each product can be included in the ID label, eliminating any human error in transcription. Basic details such as SKU code, item description, supplier, and possibly category code should be included. Labelling methods such as RFID or barcodes that can be read electronically are now standard. To ensure a smooth flow from start to finish, product descriptions and definitions must be standardized across the entire business.
Delays in goods-receiving
When visiting warehouses, we often see pallets of goods in the receiving dock. If products are palletised and identified clearly, why are they not put directly in storage? It seems there a few reasons:
- Problems identifying the product or the supplier or the quantity
- Extensive quality assurance is required at the point of receipt
- Delivery notes state the supplier’s SKU code and description only, not yours
- Supplier’s unit of measure does not correspond to yours
These goods are taking up expensive space. It also means that the length of time between receiving the poorly identified goods and them being available for sale is extended. Poor product ID leads to stock inaccuracy, which in turn leads to errors in packing, lost sales, increased complaints and returns and time wasted investigating stock issues.
Where exactly is the problem?
Many warehouse inbound operations are inefficient, but it is not always clear where the bottlenecks are. A short study to record the time spent on each task from the time the delivery arrives until the goods are stored will highlight areas of improvement. Activities include time to unload, number of lines / full pallets/cases unloaded, / units, number of part pallets/cases unloaded, labour hours spent processing goods and documentation, time taken to move to store. Such a study will show which suppliers and which product ranges make up 80%+ of labour time spent in receiving. Labour is a huge cost. Track which suppliers and which carriers create the most problems. Our experience shows that focusing on these suppliers and their product ranges can drive overall goods-inward productivity up by about 50%. It entails close cooperation between buyers and suppliers to jointly drive improvements.
Actively manage your suppliers
When items arrive with a delivery note carrying only the supplier’s SKU code and description it causes delays. Relying on your staff’s product knowledge is ineffective, temporary staff don’t have the required product knowledge anyway. One obvious solution is the standardisation of a product ID across the supply chain. It is not difficult to achieve. It requires the supplier to include your product ID data on every item you purchase in the format you need. Sometimes it does not happen because we don’t ask for it. Maybe the supplier charges for the service and we have declined. This is short-sighted. The benefit in productivity far outweighs any extra cost.
Lack of a clear unit of measure in a product ID means confusion. It is highly time-consuming in the case of mixed pallets or complex multi-SKU container loads where the units of measure do not tie-up. (We ordered 500 items in cases of 12 and we received 41 cases and 8 loose). When the ID is poor, everything slows down, it is especially damaging in peak periods.
A good “new product” process can help. A clear joint product ID is agreed with the supplier upfront, preferably with all products barcode identified before arriving in the warehouse for the first time. The product master data can then be pre-populated to enable good decisions to be made on where to locate products.
Many of the problems related to the receiving of goods in the warehouse can be mitigated by developing clear lines of communication with your suppliers and working together on areas of improvement related to product identification.

Leave a Reply
You must be logged in to post a comment.