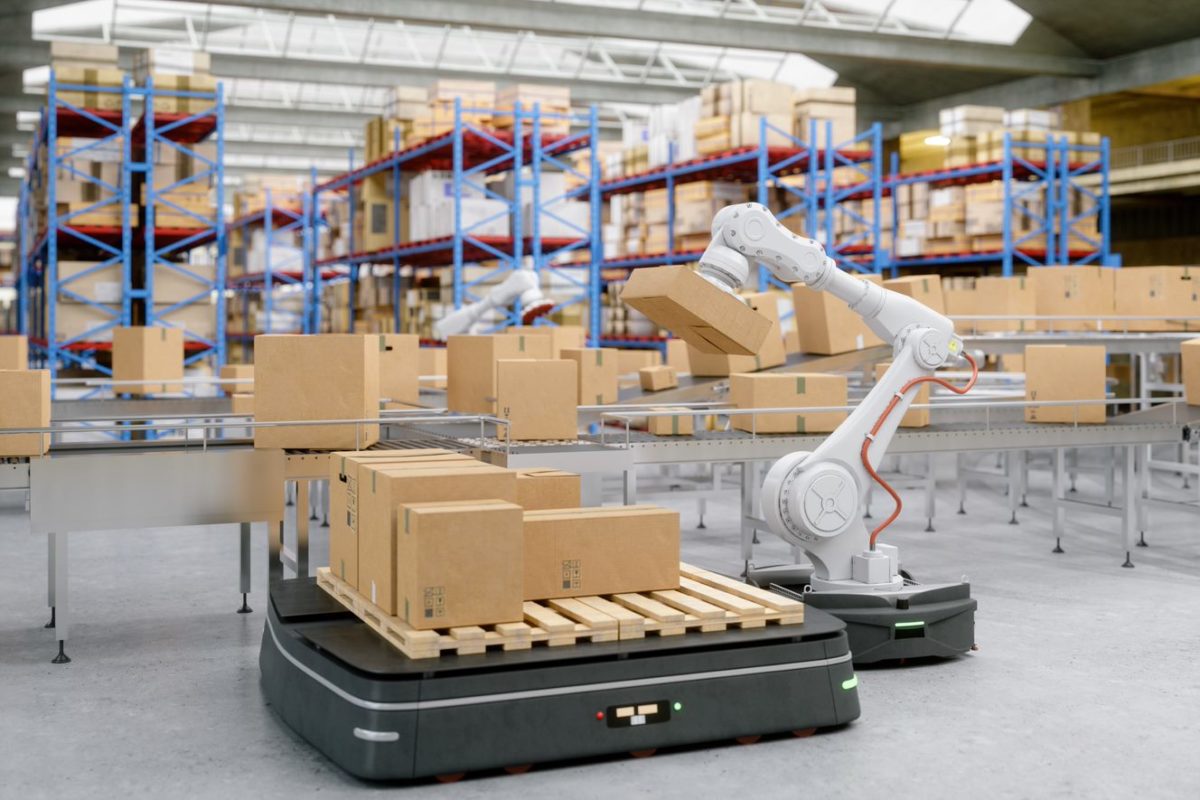
Learning From the Past, Planning for the Future: WMS must cope with changing business and technological requirements
Learning From the Past, Planning for the Future with Cold Chain Federation member Principal Logistics Technologies.
There is no doubt that many things changed as a result of Covid. But as we return to something like normal there are plenty of other pressures in the supply chain. The ongoing effects of Brexit, staff shortages, limited warehouse space, and an unstable economy are forcing businesses to assess their supply chain operations to make them leaner, more adaptable, more efficient, and less expensive. On top of this the ongoing evolution in automation and emergence of new forms of AI are likely to bring even more challenges. What are the lessons from the past three years and what can we do to plan for the future?
Build Resilience: supply chains – by and large – coped very well during Covid. While many organisations had planned and tested crisis management processes, few foresaw the precise nature of the emergency. But in the event many businesses were able to cope with the sudden and significant increases in demand that were driven by more people ordering more things online for home delivery or click-and-collect. This is due in no small part to the resilience of the physical supply chains and supporting infrastructure that had been planned and built into the system over many years. Attaining and retaining resilience is always a good way to meet future challenges.
Dealing with Fewer Staff: in almost every imaginable scenario, businesses operating a warehouse needed to cope with fewer staff during the pandemic. That meant ensuring existing processes and tasks were completed at maximum efficiency. A well-designed WMS can cope with even large fluctuations in demands and throughput in technological terms. Having the staff to cope may be a different matter. Adding capacity can be achieved through increased efficiency. The continued growth in the supply chain sector coupled with shortage of skilled and suitable staff means these pressures will remain but a well-designed and configured WMS will help.
Fast Deployment: responding to new market challenges, such as those presented by the pandemic but more generally in an increasingly fast-paced world, is a typical business scenario. Effective solutions can often be created by using – or at least starting from – a well-defined set of core features that cover most requirements. This is a common characteristic of cloud-based systems – including WMS – and for most customers these can be deployed with very little or no additional configuration. Nor do they require all the local infrastructure required by conventional or traditional systems. In particular, there is no need to install, configure and “go live” a dedicated on-premises computer to host the application. Instead, the cloud-based application is hosted and managed by the service provider. All of this means that a system can be made available to a potential user in very short order – weeks rather than months. And system enhancements are dynamically installed and instantly available so there is nothing the user needs to do.
Scalability: for established and growing businesses, such as those in ecommerce, the ability to scale applications upwards to meet increased volumes and throughput is critical. Most well-designed WMS will have a degree of scalability but SaaS-based solutions are almost always based on platforms with this capability. Modern operating systems and application architectures were designed to cope with more concurrent users than older systems which might be based on what we now think of as very old concepts. Cloud-based systems generally have fewer restraints in terms of data throughput so there should be less risk of “bottlenecks” when more users are added or there is an increase in transactions. In reality, well-designed WMS of any kind will be able to cope but it can often be simpler to add extra users to a cloud-based system.
Speed of Implementation: cloud-based solutions can generally be up and running more quickly than conventional systems. This can be useful when setting up temporary supply chains or new routes to market in response to rapidly changing demands, such as during the recent crisis. SaaS based solutions offer a wide range of standard features – more than enough for most warehouse operations – but relatively little bespoke capability. This means they can be implemented very quickly, with new users added or removed when required to provide scalability.
Cost Control: always important, but never more so that during a crisis, cost-control should always be part of the justification for WMS investment. Cloud-based solution providers generally charge monthly for the number of users, and are not subject to long term contracts, so costs only increase when they can be justified by the growing size of the operation. But they can also decrease if demand reduces. Conventional systems, on the other hand, are generally built (and priced) for a specific number of users with most costs loaded up front. Moreover, cloud-based monthly fees can be easier to justify (and may come from revenue rather than capital budgets) while the benefits and returns are easier to identify because they are more closely aligned with operational patterns.
Remote Capability: another lesson from Covid is that working from home – or more generally remotely – is possible for far more people than previously thought. During the crisis this was the one area where a cloud-based WMS stood apart from a traditional application. The applications are hosted on robust and resilient servers running in a dedicated data centre and managed by the service provider. Users access the system from any location with internet or mobile data availability using a browser or, increasingly, a dedicated app on whatever device suits – PC, laptop, tablet or phone. Users are freed to work productively from any location. In the real world, of course, people still need to be present in the warehouse to carry out the actual handling tasks. Nevertheless, remote access removes one of the major potential restrictions in a warehouse’s ability to cope during an emergency by allowing managers to maintain oversight and control even if they are unable to be in the building.
Automation: although automation has been around for some time there is no doubt that the unique circumstances of Covid gave added impetus to development and innovation. Many organisations have invested more in automation in their supply chains over the past two or three years than ever before and this trend shows no sign of slowing. At the same time, new forms of AI are beginning to deliver intriguing insights into operational trends and enable new forms of interaction between other systems, equipment, transport networks, employees, suppliers, and customers. Well-designed WMS should have industry-standard API interfaces to integrate easily with existing business applications and the ability to import data simply from a range of sources. This means they should already be able to interface with even newer technologies so that operators can integrate highly efficient capabilities into their extended supply chains but with the potential for as-yet only hinted at possibilities.
The unique set of challenges presented by Covid have evolved and merged with current economic, technological, and business trends to create a very different supply chain landscape from the one we saw in 2019. Many businesses responded well to the emergency and lessons learned can be applied to cope with these newer challenges. Having a WMS that can cope with changing business and technological requirements and interface and integrate with other systems will help.
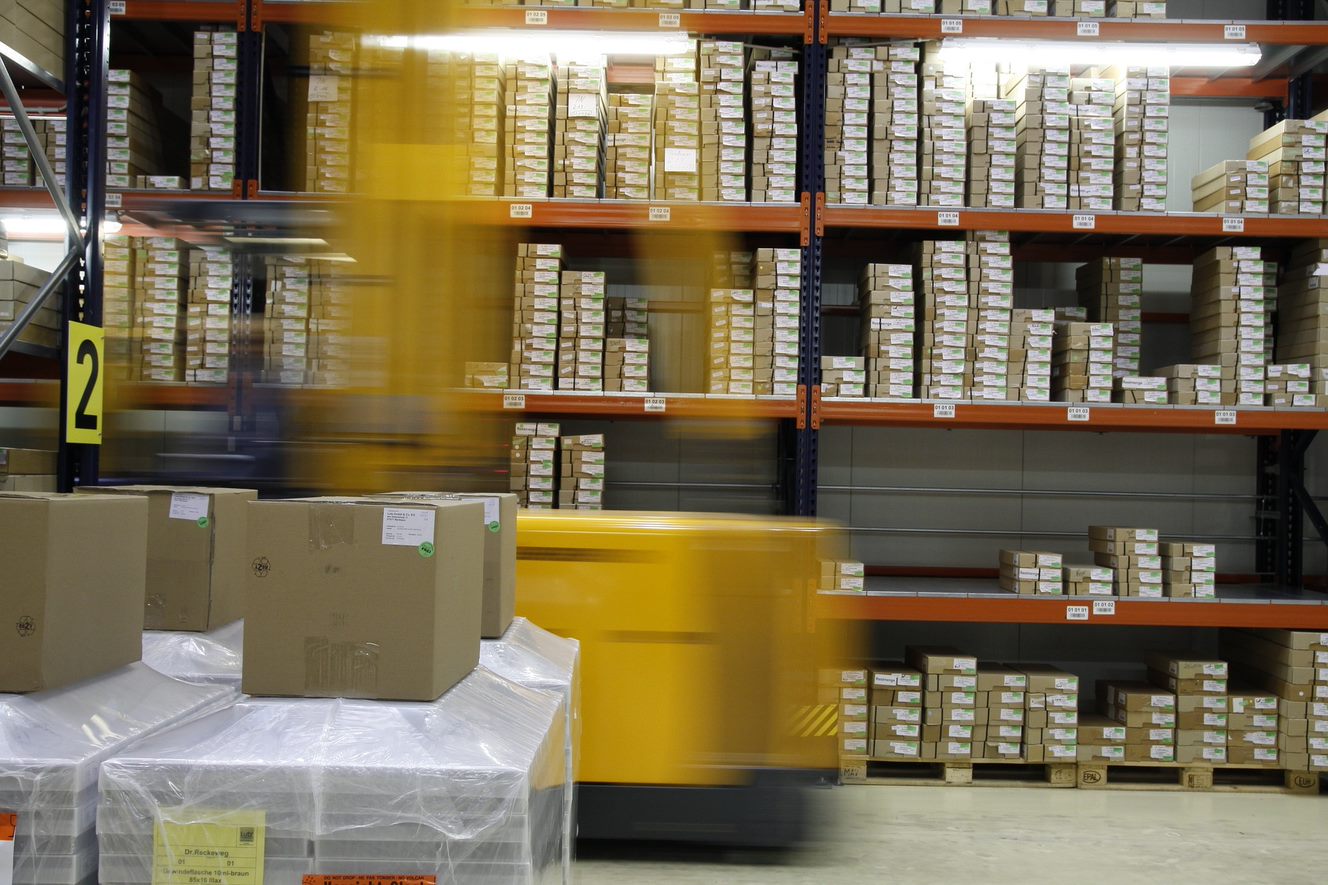
Comments are closed.