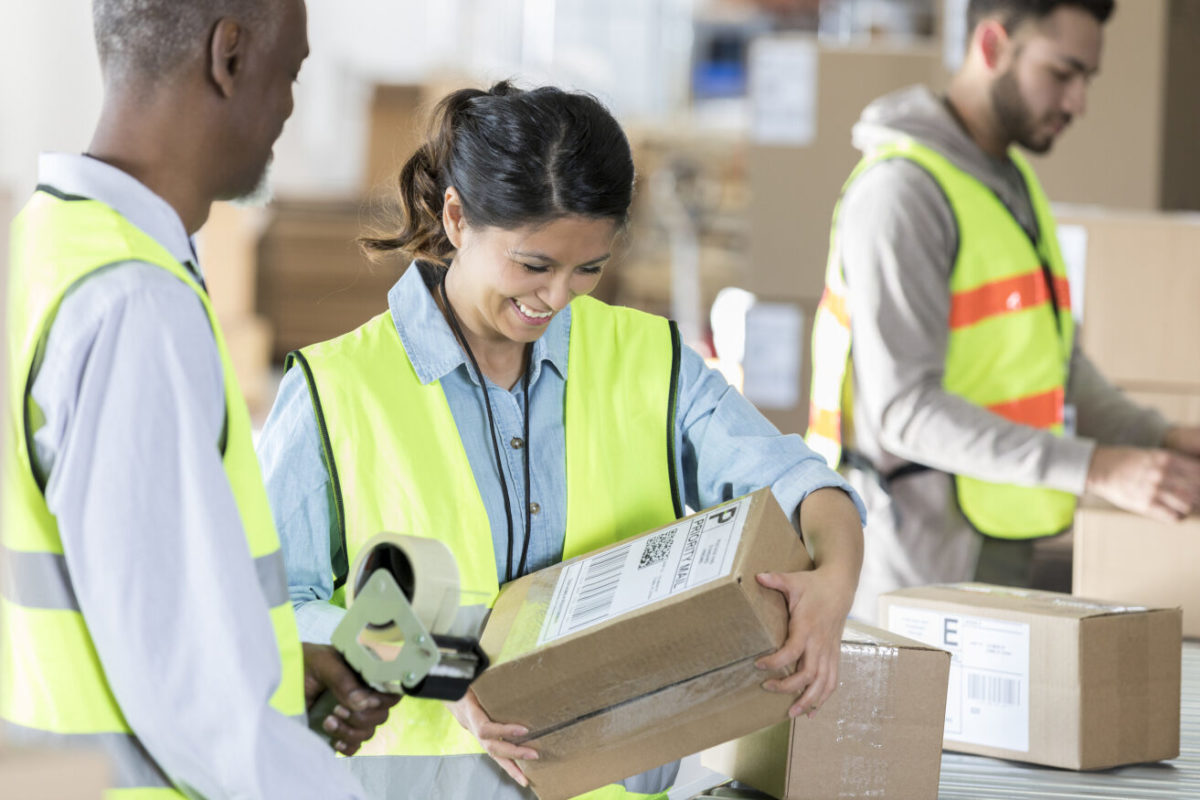
It’s Peak Season Again: Are You Ready?
The annual retail peak is predictable and manageable, and it is something we have written about previously. Very little in terms of the patterns of the peak has changed although the way retailers and their suppliers are responding may have. There is no doubt too that the peak season is starting earlier: mince pies have been on the supermarket shelves since they replaced “return to school” items at the start of September. In reality, the peak has become a series of events such as Halloween and Black Friday aimed at boosting sales during this all-important period. It is well known that the majority of retailers make most of their sales in Q4 and effective warehousing and distribution is key. What can retailers and their suppliers do to maximise the opportunities during this vital period?
There is no doubt that the ongoing economic climate continues to force everyone to focus on the cost controls and efficiencies that help ensure competitive purchasing prices for consumers while allowing that all important profit margin. A recent industry report looked at how European retailers and their supply chain partners are planning to navigate the 2023 peak season. The results suggest that businesses that have planned well and have robust processes in place will be able to cope best. Over three quarters specifically said that having a WMS or OMS will help them prepare their warehouses to be more profitable during this year’s peak, presumably by being better organised and more efficient. There is no secret than a properly configured WMS can support a business through seasonal peaks and it is something we have written about ourselves before.
The overriding priority during peak is to maximise the availability of items for customers to buy. That means having items “on the shelf” for a conventional shop or being marked as “in stock” for ecommerce businesses. Assuming the business has planned its supply chain carefully and ordered the right items – and volumes – from suppliers, this will come down to deploying efficient warehouse management and fulfilment processes to:
- manage fluctuating demand levels dynamically for best use of resources in the warehouse
- ensure maximum number of orders processed and shipped each day
- compile orders with total accuracy
- maximise customer opportunities to buy
- plan routes and loads effectively to optimise utilisation of delivery vehicles
- get products to customers on time and in full
- Integrate with their internal and external payment and shipping systems
There is another broad reason why it is vital to ensure supply chain operations work properly during the peak: customer satisfaction. Getting orders right, and right first time, is key to keeping customers happy. That is true at any time of the year but may be especially so during the run up to Christmas when there may be little or no time to put something right if it all goes wrong. And with so many retailers doing so much business at this time it follows that they are dealing with more customers, perhaps for the first and/or only time. So they only have one chance to get it right. In both cases, providing customers with a great experience helps to ensure not just good ratings and recommendations but can also instil the loyalty that leads to repeat business and additional orders later on. Apparently around three quarters of customers say they would not deal with a business that has let them down. Having the right WMS and fulfilment processes in place is a good start but it also means having efficient processes to deal with returns and replacements can be just as important. Perhaps more so, because while customers expect you to get their order right how you deal with any errors is likely to be noticed even more. Offering customers a straight replacement or like-for-like alternative can help avoid disappointment on the big day and helps the business by reducing the need for a simple refund. According to some, a good returns process can reduce the need for refunds by almost a third. Having processes in place to respond and meet customers’ needs quickly is imperative.
Clearly it helps if supporting technologies such as WMS and transport management are working properly, and together. But not at any price. In the survey mentioned above, just over half of the businesses surveyed said that managing costs is their priority for the peak season. Over a third also said that rising prices – as defined by higher inflation – is also a concern. This impacts businesses in two clear ways. First, costs to the business have to controlled because this helps to mitigate any effects of price rises that are beyond their control. Second, some of those savings can be used to limit any price rises seen by customers and so support sales volumes. Using the available WMS technologies and systems to maximise productivity, efficiency and throughput volumes can all help.
Another trend identified by the survey was that companies are investing more in automation to cope with fluctuating labour patterns. In fact, the increase among those surveyed was fivefold compared with last year. That is clearly significant and it is also something we have written about before. As we have said, any decent WMS should be capable of interfacing and integrating with automation technologies.
Automation aims to address one of the biggest challenges facing warehouse operators: recruiting suitably skilled staff to meet the relatively short-term demands presented by the annual peak. Many of those in the job market do not have the required skills to be productive in the warehouse from day one. When businesses choose recruitment over automation, providing basic training is essential. But the costs and time required need to be balanced against the likelihood that the people concerned will have left by New Year. Warehouse technologies can help here because they generally becoming easier to use, with simpler commands and instructions and familiar devices and interfaces. That will shorten and simplify training and induction and reduce the risk of errors, all of which will increase productivity and efficiency and shorten the time to repay any up-front investment.
There is also a case for increasing the performance and efficiency of existing employees so there is less need to recruit temporary staff. This is part of a longer-term trend for businesses to invest in their permanent workforce. Again, WMS and similar technologies can help by enabling the flexible working and real time adaptability of warehouse operations so that employees are more productive for more of their shift without becoming overburdened.
None of this is likely to be possible this year, however. Peak is upon us and the majority of businesses will already be working through the increased workloads and volumes, using the systems and applications they have in place. There may be little room for flexibility this year but there is no reason what you cannot start planning for next already.
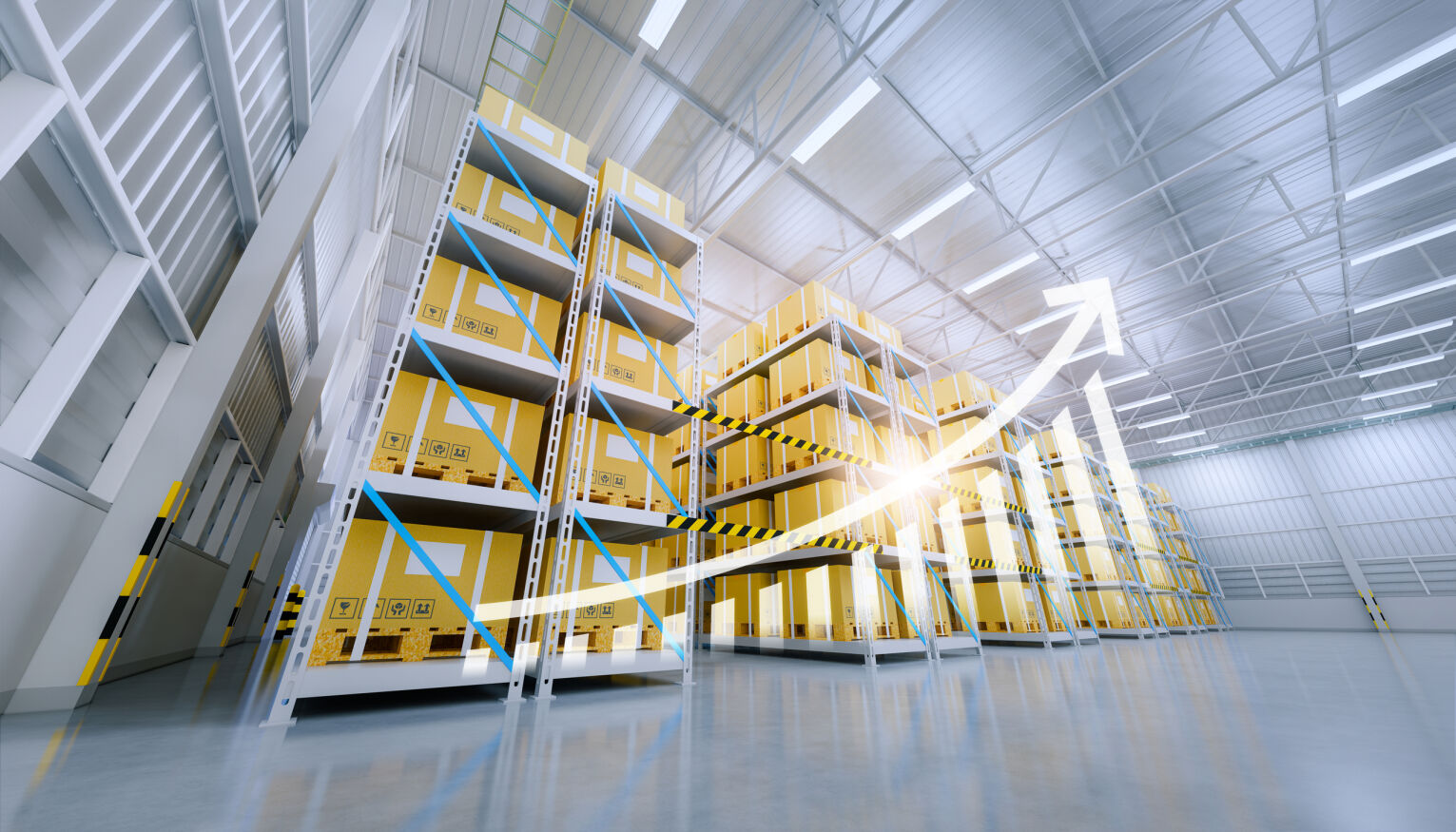
Comments are closed.