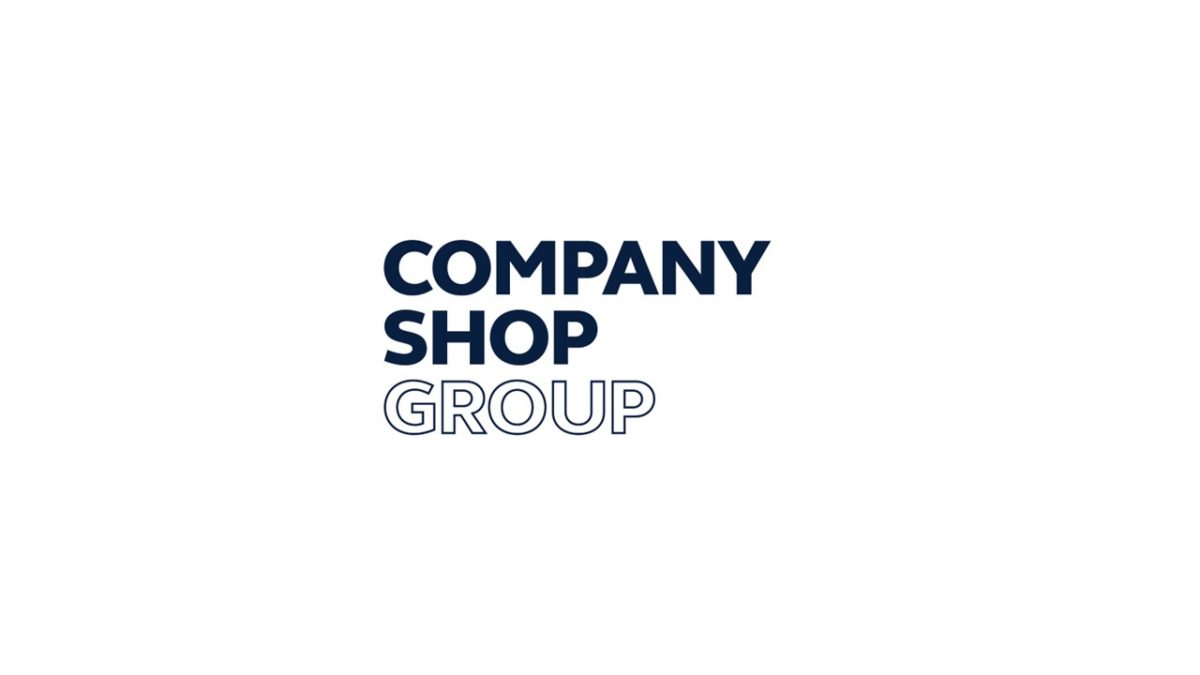
The UK cold chain must consider enhanced redistribution agreements with retailers, in order to maintain ambitious environmental progress
The UK cold chain sector has a strong track record for embracing ambitious sustainability and net zero targets. This is supported by the Climate Change Agreement which the Cold Chain Federation (CCF) remains a proud champion of.
Whilst improving energy efficiency and reducing emissions is a large focus for the cold and third-party logistics sector, the impact of food waste on the climate cannot be ignored either.
The UK’s cold chain plays an integral role itself in preventing and reducing food waste, due to its resilience and flexibility. Similarly, the innovative nature of the temperature-controlled provision offered to customers today means that food and products can make it safely and efficiently from source to store.
However, from working at the heart of the supply chain, we know that even more can be done to ensure that food is reaching people’s plates as intended, whilst unlocking the true economic and environmental value of products. One simple way for cold chain businesses to achieve this is to reconsider their existing arrangements with retailers when it comes to the products that are no longer deemed fit for purpose.
In the same way that a product’s journey is mapped out from being processed, packaged, stored, transported, and delivered, the same clear and forward-thinking approach is required for products that have become surplus. Within the FMCG supply chain, we know surplus can be inevitable, be it due to forecast inaccuracies, issues with minimum order quantities, road network delays or simply the weather. However, it needn’t become waste.
For the cold chain and third-party logistics sector in particular, the same applies for products held in consolidation centres that have dipped below the Minimum Life On Receipt standards set by the retailer. Currently, much of this stock is needlessly thrown away because of the existing redistribution arrangements – or lack thereof – between retailers and manufacturers, and third-party logistics providers.
Cold chain businesses can navigate this challenge by collaborating with retail and manufacturing clients to agree a redistribution process for such products. For example, rather than paying to have good products disposed of as default, businesses can instead receive a financial return by using commercial redistribution routes such as Company Shop Group, which will also help to generate enhanced social and environmental good. The Group also has own label approval for all major retailers and so once a logistics provider makes a redistribution agreement with a retailer to use Company Shop, they will not need to seek approval to redistribute stock again. Instead, stock can be diverted straight to the Group’s two distribution centres in South Yorkshire and Leicester, or can be collected directly, making for an even more efficient alternative supply chain. Products can then fulfil their intended purpose by feeding people first.
By implementing this additional arrangement as part of contracts and arrangements with retailers, businesses in the cold chain can continue to uphold their ambitious societal and sustainability commitments, whilst avoiding otherwise costly waste streams at this financially challenging time.
For a corner of the sector which is renowned for its innovation and versatility, we are challenging the industry to reconsider its existing supply chain partnerships so even greater strides can be taken towards ensuring no good food goes to waste, together.
Owen McLellan, Managing Director of Company Shop Group
Comments are closed.