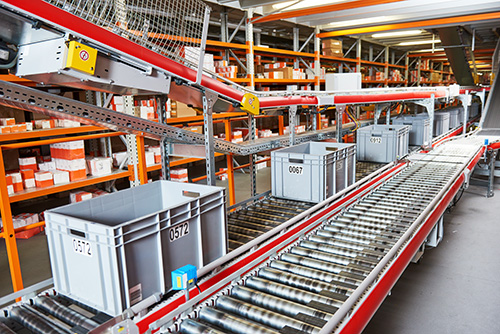
Warehouse Management Best Practices – The key to an Efficient Supply Chain
Fulfilment centre, distribution centre or warehouse? Whatever we name it, operating such a facility is a major expense. The disruptive events of the past two years have created new challenges for both capacity and staffing. The growth in e-commerce, whether B2B or B2C, has caused us to review and improve many traditional processes. What worked well previously may no longer be fit-for-purpose. Poor design and layout impact efficiency leading to higher operating costs and reduced service levels. Warehouse operations are becoming more complex and now require the use of automated equipment and other technology tools, including a warehouse management system (WMS), to drive efficiencies. Cold Chain Federation member The Supply Chain Consulting Group (SCCG) help to apply best practices.
What is warehouse management?
Warehouse management involves applying principles and processes to ensure the efficient daily operation of a warehouse facility. This includes receiving goods, organizing warehouse space, scheduling staff, managing inventory and fulfilling orders. Effective warehouse management involves integrating these processes to increase productivity and contain costs. Warehouse management is a key link in the supply chain – connecting the supplier to the customer.
Benefits of an efficient warehouse
A satisfied customer is blissfully unaware of the behind-the-scenes efforts to get their goods delivered in full, and on time. Efficient warehouse management is where all warehouse processes run as smoothly and accurately as possible from the receiving of goods to their dispatch. Streamlining storage space, quickly fulfilling orders and coordinating communication with suppliers and carriers are all key processes. Optimizing involves fine-tuning each individual process such as storage, picking, packing and streamlining how they work together. An optimized warehouse provides a high-quality service at a low cost. Achieving this can be a complex task which is why we need the help of technology. Warehouse management is as much about data and information as it is about automating processes.
What Is a warehouse management system?
A warehouse management system (WMS) is a software solution that simplifies the complexity of day-to-day warehouse operations. It eliminates manual tasks and guesswork and harmonizes processes to save time and money. Inaccurate inventories, customer service issues and pressures to continually reduce costs will make the decision to consider a WMS an easy one. Data helps warehouse managers identify areas of improvement and track progress at every stage from receiving to dispatch.
There are many WMS solutions on the market that have different functionalities depending on the business or industry they serve, e.g., there are specific solutions geared to e-commerce and its many variations. Solutions can either cloud-based or installed on-site, all with a wide range of available functions that include:
- Sourcing and procurement
- Receiving/Put away Management – Using rules-based instructions, the picking process is shortened by allocating locations to items based on their demand and sales frequency.
- Forecasting – Historical data is used to analyse demand, forecast sales and create efficient daily operating plans.
- Inventory Management – real-time visibility into inventory location and quantity is achieved using barcoding/RFID automated labelling
- Shipping and transport: important shipping documents are generated e.g., bill of lading, packing list, shipping labels, etc.
- Returns Management
A WMS can bring further benefits
Real-time reports are generated using the data created from different operations across the warehouse to help identify problem areas and mitigate risks. Most WMSs can be integrated into existing internal ERP systems or with other software solutions at third-party suppliers and carriers.
Will a WMS provide a return on my investment?
To justify your decision to source a WMS, the cost, the payback period and the benefit must be quantified to establish ROI.
- Where are the problem areas? They could include inventory accuracy and carrying costs, staff productivity, poor space allocation, stock-outs and customer service complaints.
- What are my current costs and where am I losing money? How do I compare to others in my industry? The savings associated with the reduction of inventory levels may themselves justify investment in a WMS
- What savings and benefits can I achieve? Better utilization of staff, less shrinkage, less obsolete stock, faster speed of picking and packing, leading to improved customer service.
- How much will a WMS cost? Calculations will depend on the level of functionality required, whether the solution selected is in-house (extra hardware, maintenance and storage capacity) or cloud-based (license fees, support costs). Whichever solution is selected, there are costs of system testing, implementation, and staff training.
Considerations when selecting a WMS system
The first step is to research the available WMS that work well in your type of business or industry, taking customer references. Consider the vendor’s track record, size, financial stability, and its approach to maintenance and customer support. Look for a WMS that:
- Seamlessly connects to other logistics partners systems
- Is user friendly with an easy-to-understand dashboard
- Is compatible with your internal systems and equipment
- Delivers verifiable return on investment (ROI). This can be calculated by measuring results such as:
- X time saved per hour
- X percent improvement in accuracy or reduction in errors
- X pounds saved or recovered
- X increase in order processing speed or throughput
There are three general principles that, when followed, will improve your warehouse management operations: know your business’s specific or unique characteristics, have an effective WMS system in place and be flexible and resilient when things go wrong.

Comments are closed.