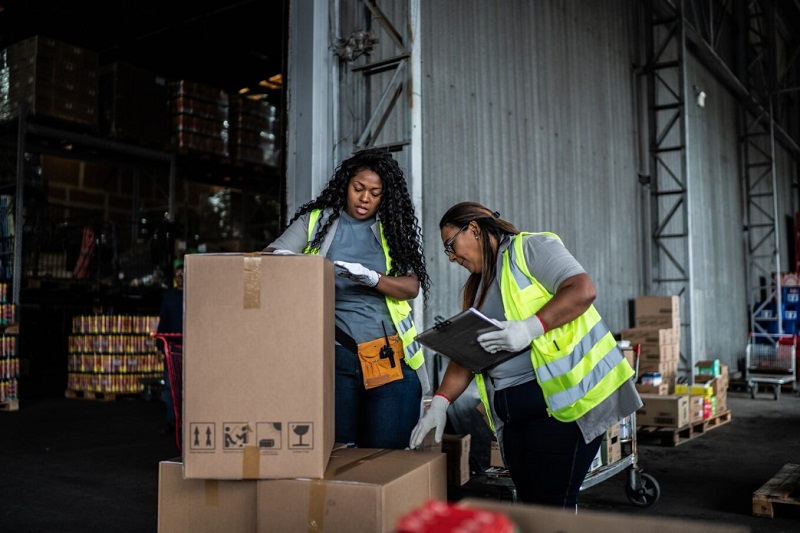
Managing Peak Returns: WMS Can Help
If the run up to Christmas represents the busiest time of the year for most retailers, January is likely the time of peak returns. Items bought as gifts in the quarter before Christmas and then handed over on the big day are going to be returned soon after if there is any kind of issue. What does this mean for warehouse operators and what might they need to do to process these items quickly and efficiently? Can warehouse management software help?
The are many reasons why an item might be returned, including a fault or because it is unwanted. Many retailers include the ability to return an item with few if any questions asked as part of their offer. On top of this retail law, particular that applying to online sales, requires that most items can be returned on request. All of this encourages returns and the result is that the number of returns across the retail sector has never been higher. According to CBRE, returns cost British retailers around £7billion each year and each returned parcel costs a retailer around £20 in shipping, warehousing and repackaging costs. This could be around 10 per cent of the retailer’s overall supply chain costs. Statista conducted a survey that suggests around two fifths of customers who placed orders for ten returned two or three. The University of Southampton’s Product Returns Research Group (PRRG) reports that 70 per cent of returns arise when customers change their minds and that these cost an average £11 for an item worth £89.
The scale of the challenge is clear and can affect warehouse operations in several ways. For example, it can lead to a backlog of returned items that need to be processed, which can slow down the overall supply chain process. Additionally, it can lead to an increase in labour costs, as more workers may be needed to handle the increased volume of returns. These challenges are likely to be at their highest in January when returns peak.
Traditional retail supply chains tended to focus on the initial fulfilment but changes in the market and regulations shifted the balance as returns have become easier and more common. And returns are inevitably more complex. For a start, all items must be checked and processed as they arrive back at the warehouse, with less predictability than with incoming stock. They probably arrive in ones or twos, in a variety of packaging, and delivered by a range of carriers. Even when returns represent a small proportion of the overall stock, they are likely to involve a higher number of handling tasks and data capture transactions.
There are several things the warehouse will need to do. Initial tasks could include, for example, confirming receipt and verifying it against customer information (to ensure the customer has returned what they said they would). Checking whether packaging is intact or if items have been opened, used, or worn is also important at this stage to help determine if items can be returned to stock ready for resale. Items with damaged packaging or which have been opened or used might be subject to further checks, remedial action, or designated as unavailable for future sale. Items returned as faulty will need to be sent for repair, recycling, or disposal.
All of this can be done by hand or using manual processes. But it is all so much easier if the returns process is built into the warehouse management software (WMS). The WMS will oversee the processes required to accept and process the return, helping users to make necessary decisions, and ensuring the consistency, accuracy, and discipline that comes with such applications. In many cases these decisions are automated – or at least automatically applied – to minimise human intervention and to interface with other business applications.
After an item has been accepted, there are further actions the WMS can support. Depending on its condition, the item could be made available for sale and re-allocated to a picking face, redirected to areas designated to rework, repackaging, repair, or disposal. At the same time, accepting the return can prompt other applications to send a receipt advice to customers, generate pick instructions for a replacement, issue a refund, and so on. Some of these actions might even be prompted as soon as the designated carrier collects the item from the customer. The WMS will be involved in some of these subsequent actions, for example where replacements are sent out.
Dealing with returns efficiently has positive benefits for the business in terms of reducing overall costs and improving productivity. It will also have a positive impact on customer service and perceptions because it helps the business to respond to their requirements quickly and in line with expectations. Indeed, it might also add value to the business if the returns process is perceived to go “above and beyond”, lead to further opportunities to sell, or enables some form of unique offer for the customer. But with the number of returns increasing – and peaking at the beginning of the year – all of this can also add to the burden on warehouse infrastructure and hard-pressed staff. Using a WMS should enable the efficiencies and productivity gains that minimise these burdens and experienced application providers will know how to configure their systems for optimum performance. Smaller and growing businesses in sectors such as ecommerce and retailing may find that SaaS-based WMS – such as ProSKU – offer a faster, simpler, and less expensive implementation path than a traditional “hosted” system. Whatever type of WMS is chosen there are, in general, five areas where efforts might most usefully be directed include:
Implement a Returns Management System: a specialised returns system within the WMS can support efficient processes and decision making and provide an effective interface with staff, automated systems, and interfaces with other business applications such as an e-commerce site, sales order processing, accounts, and more. Many modern WMS include these facilities as standard or they can be supplied as part of a module.
Automate Data Collection: barcodes, QR codes, RFID and other technologies can be used to identify and track returned items to minimise human intervention and automate many of the related processes. This can help to improve efficiency and productivity with reduced labour costs.
Remove Manual Data Entry: hand-held devices such as scanners, computers and even smartphones can all be used to read data from incoming returns. Items are identified immediately and data is accurate and consistent with reduced potential for errors.
Optimise Warehouse Layout: configure the warehouse to deal with returns more efficiently. This might include, for example, dedicated areas for accepting returns or special locations to store items before they are processed further.
Ensure Adequate Staffing: make sure that there are sufficient numbers of warehouse staff to handle the increased volume of returns during peak seasons. If it is not possible to allocate staff full time to returns there are other options. For example, many modern WMS include the ability to prioritise actions or dynamically allocate tasks. In this way warehouse operators can ensure returns are dealt with when required but allow staff members to deal with other tasks when workloads require.
By following these best practices, warehouse operators can optimise their returns management process, increase customer satisfaction, and reduce losses.

Comments are closed.