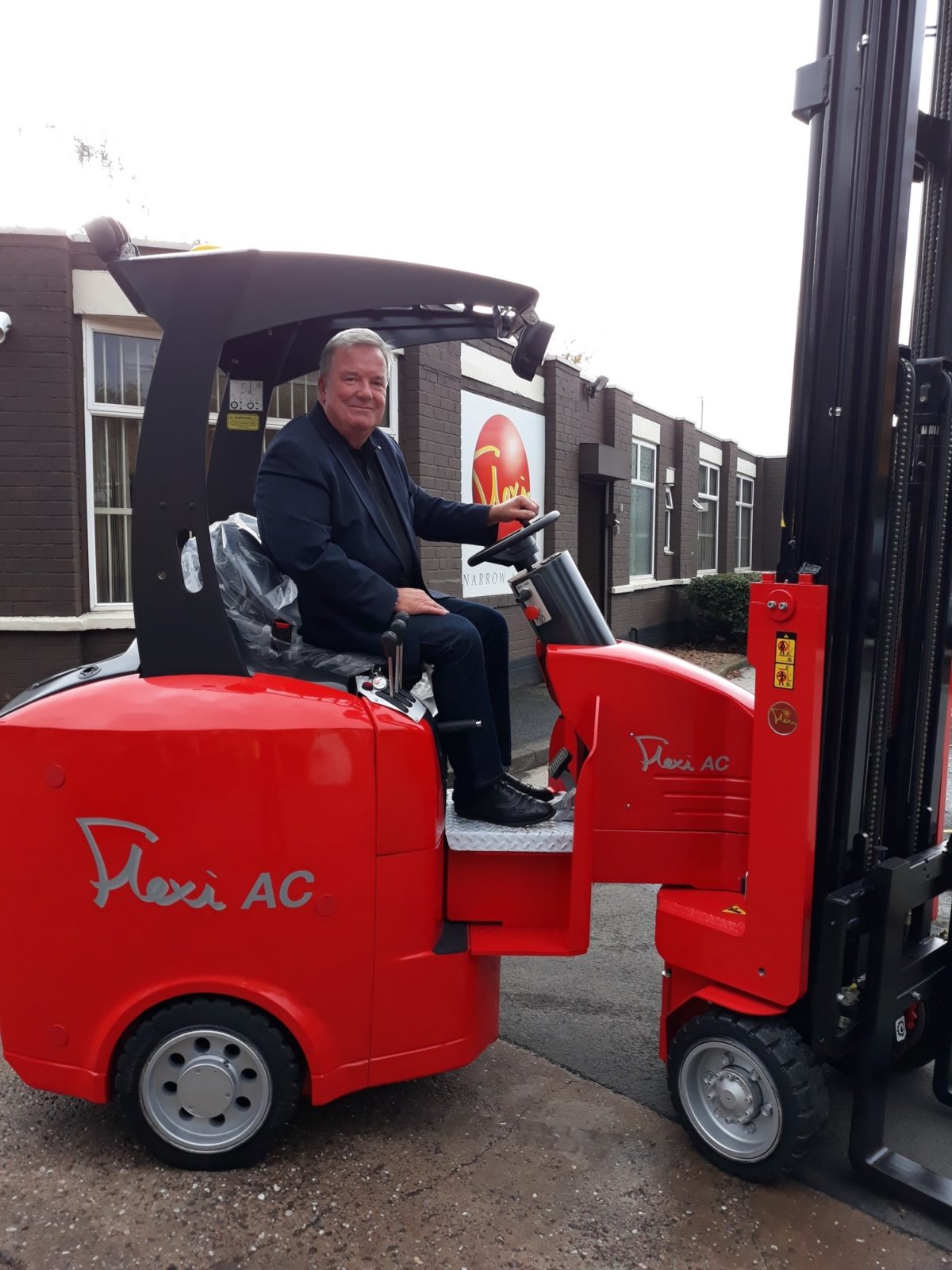
Grocery and retail DCs are changing their order picking strategies
The growing popularity of online and convenience store shopping together with the emergence of automated order picking robot technology has caused many grocery and retail DCs to rethink their intralogistics strategies and place less emphasis on ‘zone picking’, says Cold Chain Federation Member Narrow Aisle Ltd’s John Maguire.
Out of the zone?
Of all the processes involved in modern warehousing, the ability to quickly and accurately collate picked goods with an efficient order picking regime has the greatest impact on a warehouse or DC’s performance, costs and ability to deliver customer satisfaction.
And it has long been accepted that those storage facilities which serve the grocery and retail sectors can achieve optimum order picking efficiency by deploying a picking strategy commonly known as ‘zone picking’.
In simple terms, ‘zone picking’ involves dividing stock-keeping units (SKUs) into different product zones within the store and assigning pickers with pick lists to work within each zone. Each picker is responsible for picking all SKUs located within their area of the store for each order; in this way, the roll container or pallet is loaded with similar product types to aid efficient decanting into shelves on arrival at a retail store.
There are a number of benefits attributed to zone picking. For example, because pickers remain in their assigned zones rather than traveling around the warehouse, operative travel time between picks is minimised. In addition, as they work within a smaller area of the store, pickers become more familiar with the SKUs and pick locations within their zone and, as a result, pick rates are faster and more accurate.
However, shopping habits and consumer preferences are changing, As a result, convenience stores – smaller, local shops serving the community – are flourishing to the extent that many retail analysts are predicting that the days when shoppers stocked up on keenly-priced ‘buy-one, get-one-free’ offers in superstores could be coming to an end.
Indeed, in the five years between 2015 and 2020, convenience sector sales grew by an average of 2.6%, according to Lumina Intelligence UK’s convenience market report. In 2020 (the year of the pandemic, if anyone needed reminding) sales leapt 6.3% in just 12 months and, looking ahead, the sector is expected to be worth £47.1bn by 2024.
The growing popularity of the convenience model has caused order picking techniques to be reconsidered within many grocery DCs. Convenience stores require more frequent stock replenishment with fewer items. This means that within the DC or warehouse, pickers are picking far less items per line visit but picks are made more frequently. Picking fewer items more often also requires operatives to travel greater distances than in a zone picking scenario – not least because it makes sense to move similar product types further apart to avoid congestion in the picking aisles. And, of course, more ground level picking locations are required.
To optimise picking efficiency at storage facilities where fewer but more frequent picks are required, new technology in the form of AI-driven picking robots – or Cobots as they are sometimes referred to – is increasingly being adopted.
Developed to maximise productivity and lower cycle times, automated robotic picking technology means workers no longer have to push heavy roll containers or walk behind slow-moving carts that are clogging the aisles. Unproductive walking time is eliminated too – which significantly improves workplace ergonomics and health and safety.
The intelligent software at the heart of some robotic picking systems also helps to improve pick speeds by constantly reconfiguring the optimum location for picking faces based on data fed back to the site’s warehouse management system. By identifying fast moving items as well as the slower lines the most time-efficient pick locations can be allocated within the storage system.
This continuous planning process allied to the speed that the robotic devices can travel between picks, reduces congestion in the aisleways and eliminates the need for one picker to overtake another within the aisles. This allows the width of the storage building’s aisleways to be significantly reduced, which, in turn, increases storage capacity and adds to those all-important ground level product locations.
Of course, if aisle widths are reduced, the materials handling equipment used to replenish the bulk storage areas above the ground and first level picking locations must be capable of operating safely and efficiently within the narrower channels and interfacing safely with pedestrians and robots alike.
The Flexi Truck range of articulated forklift truck-based intralogistics systems can be the ideal choice for sites where robotic picking technology is deployed. Capable of performing in aisles measuring just 2.0 metres wide and with the ability to lift palletised loads to heights of 15 metres, Flexi Trucks are able to operate during the pick cycle – unlike traditional man-up guided VNA machines, for example, which require the storage cube to be free of pedestrian or other truck traffic at all times.
There is no doubt that higher throughputs, greater picking accuracy and increased emphasis on ground and first level picking are now the key goals at many sites. As a result, the type of materials handling equipment used within the modern order-picking environment is changing too. Automated picking robots deliver many advantages but some of these benefits can be lost if they are not complemented with the most suitable materials handling equipment.
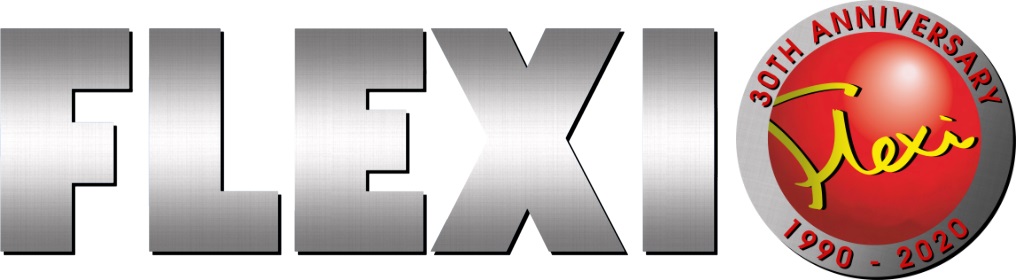
Comments are closed.