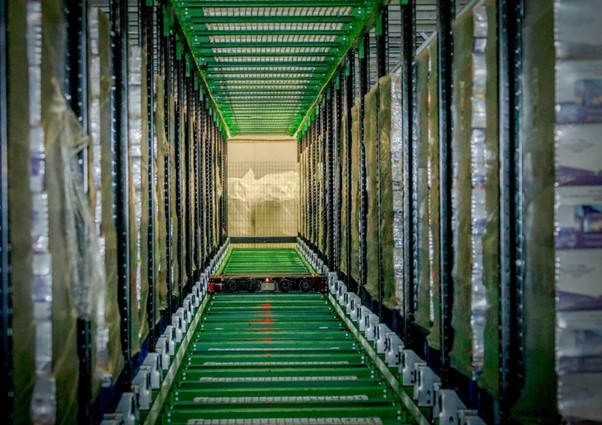
Automation in the Cold Storage Supply Chain
Cold Chain Federation Member Moffett Automated Storage has put together this article for automated storage systems.
In the supply chain industry, industrial robots and automation are replacing some of the roles in which companies are struggling to find workers. Operational processes are being streamlined by these automated devices, also known as automated storage and retrieval systems, or AS/RS, in a variety of industries.
And whilst this is a growing trend amongst the entire supply chain, one particular industry which is reaping the rewards of AS/RS Systems is that of the Cold Chain.
As a whole, the cold chain, and the requirement for goods to be delivered from the cold chain, is a higher risk industry in comparison with the ambient cold chain. Companies are constantly under pressure to meet deadlines, and avoid any mistakes, operational downtime, or delay due to the nature of the product, and the impact that failure to deliver will have on their business. Typically speaking, the cold chain deals with two main industries: Food and Pharmaceutical, both of which has strict guidelines and regulations around the timing of deliveries and the importance that zero contamination occurs.
Reducing the risk of Contamination:
Contamination and spoilage provide substantial challenges to the cold storage supply chain. With an ASRS system in cold storage, there is no need for human interaction inside the cold storage. This means no individual will have physical access to a pallet without placing an order within the warehouse WCS or the WMS. This means companies can assure 100% traceability of each pallet within the warehouse and ensure that no tampering with the pallet has taken place. By eliminating the human interaction within the cold store, not only are you eliminating the risk of spoilage or contamination, but also you are creating a safer environment for your employees, not being exposed to the harsh temperatures of the cold store.
Strengthening Accuracy in Staging and Delivery:
Outbound shipment accuracy is increased through automation. Humans aren’t perfect, let’s face it. Even the most careful workers occasionally make mistakes. Automation will always and without fail complete their tasks accurately, ensuring that only pallets ordered will be outbounded for each particular load. Orders can be prepared in-rack outside of operating hours, to ensure the fast and accurate staging of loads from the warehouse. Every load is fully customisable and schedulable with the capabilities for the automated system to operate 24/7 without the need for any personnel in the warehouse. Within Moffett Automated Storage, this is known as outbound buffering of pallets.
Reducing Energy costs on a per-pallet basis:
With ASRS Systems, the increase in storage density in comparison with traditional storage solutions is huge. Storing significantly more pallets in the exact same space can lead to significant energy cost savings for companies on a per-pallet basis. This also helps the company become more sustainable, with less energy needed to cool each pallet. Also, by eliminating the constant flow of large vehicles driving in and out of the cold store, the heat loss during transferring is also significantly less. Rapid envelope doors, or interlock doors, that are only the size of the largest pallet, can be implemented into cold stores to ensure that the heat loss is minimised. Again, this can lead to savings in energy costs. Additionally, because automated equipment reduces the need for human employees, energy savings could happen due to the reduced dependence on lights throughout the cold store.
Cold Chain Federation Member, Moffett AS/R System:
The Moffett AS/R System and our 4D Taxis have significantly contributed to the rise of automation and ASRS Systems seen in Cold Storage. Our system can operate from +50 degrees Celsius to -28 degrees Celsius. They also see an increase in storage density of around 65% compared with traditional storage solutions and are tailor-designed around all requirements of the warehouse. Throughputs can be adjusted by adding extra taxis, and inbound/outbound areas can be located in different areas of the building depending on the requirements.

Comments are closed.