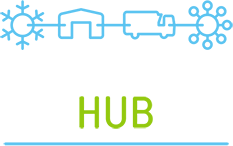
All the latest news from our storage, distribution and associate members. The hub is the place to find out about company developments, people moves and product innovations.
If you have news you want us to showcase email [email protected]
Filter your articles
Food and Drug Costs Predicted To Soar as NIC Increases Bite
Published on November 11 2024
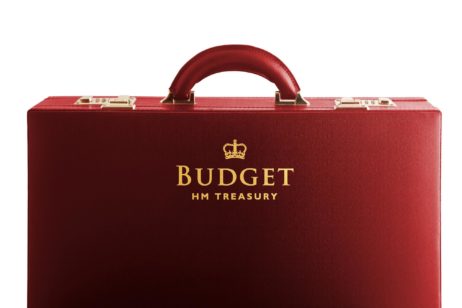
NEW GUIDE TO HELP BUSINESSES MANAGE FOOD SAFETY IN THE COLD CHAIN
Published on June 17 2021
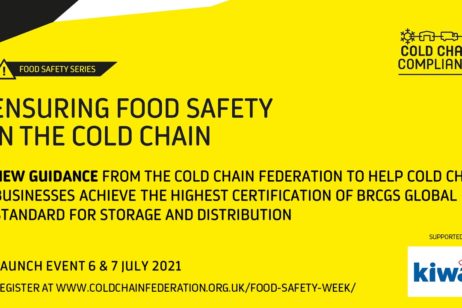
Waste Not, Want Not
Published on June 12 2019
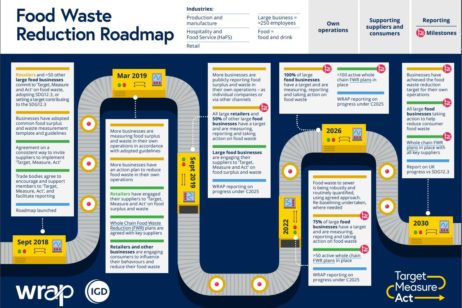
The Future According to FSDF
Published on April 2 2019
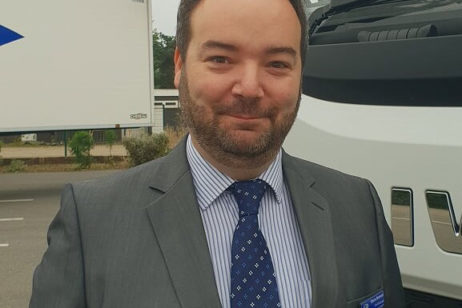